ししかわです。
社員研修の一環で、マイクロマウスを自作して大会に出場します。
今回は自作マウス「M5Mouse」の外装を作るまでの試行錯誤をダイジェストでお届けします。
外装の作成では次のステップを繰り返しながらモデルを徐々に改善していきました。
- Fusion360でモデルを作る
- 3Dプリンタで印刷してみる
- 印刷物を自己レビューする
- 自己レビューに基づいてモデルを修正する
自己レビューで確認できること
特に私のような初心者にとって、機械設計を一発で成功させることは困難です。幸い会社から貸与された3Dプリントを自由に使えるので、設計途中のモデルでもどんどん実際に印刷してみて自己レビューを行います。
この自己レビューはかなり効果がありました。実際に印刷してみないとわからないことが色々ありました。特に次の事項は印刷物を使った確認が役に立ちました。
- ちゃんとプリントできるか。あまりにも基本的ではありますが、例えば部品が小さすぎたり細すぎたりすると、プリンタ側の精度が足りずに出力されないことがありました。
- 部品の干渉が無いか。CADで全ての部品を設計しきれたらよいですが、例えばモータから出るケーブルがモータマウントと干渉するなど想定外のミスがありました。
- 組み立てと分解が簡単にできるか。私の場合、CAD上で部品の干渉が無くても、実際に印刷すると「どうやって組み立てるの…?」というモデルができてしまっていました。
- 強度は十分か。外装の厚みによってどれくらい強度が変わるかの間隔がまだ掴めていなかったので、厚みを色々変えながら組み付けて確認しました。
試行錯誤
3Dプリンタは会社貸与のAFINIA H400+を使いました。
こちらは「子供が触れない場所」を探し求めてたんすの上に辿り着いたAfiniaちゃんです pic.twitter.com/yWf2HwOIIn
— ししかわ (@meganetaaan) April 1, 2020
設計が固まるまでに全部で5回サイクルを繰り返しました。1サイクルあたりレビューで2時間、設計変更に2時間程度かかっています。一度プリントのジョブを投げてしまえば印刷中は他のことができるので楽です。
1回目
最初のトライです。この時外装はまだ設計途中だったので、モータ周辺が組み立てられるかを確認するために次の部品を出力しました。
- モータ基板のモック
- モータ(FAULHABER 1717)を基板に固定するためのモータマウント
- スパーギヤ(別途購入予定だが、大きさを確認するために出力)
- モータマウントが薄すぎてサポートを剥がす時に壊れてしまいました。特に画像手前側の細くなっている部分が弱いのでもっと太くする必要があります。
2回目
- モータマウントを厚く太くしました。
- 部品が折れなくなりましたが、基板に垂直に固定することが難しそうです。
- 箱状の外装の底部にモータドライバの基板を取り付ける予定でしたが、基板と外装の間のクリアランスが不十分で底にはめることができませんでした。
- また、底から外装→基板→モータマウントの順で固定するよりも外装→モータマウント→基板の順(つまりモータ基板が箱の中央付近に来る)のほうがモータ周辺を安定して固定できそうという考えに至りました。
M5Stackを載せた様子。「おお、それっぽい!」とテンションが上がります。
3回目
- モータマウントを改修してモータ全体を包むようにしました。
- 実際にモータを組み付けるとモータから伸びるケーブルが部品と干渉して固定できませんでした。
- 外装→モータマウント→基板、の順で固定するようにしました。
- 外装にセンサ用の穴を開けました。
- 写真を社のチャットに貼ったところ「センサの位置はなるべく下のほうがよい」というアドバイスを先輩から受けました。
4回目
- センサの穴を下に下げました。
- 基板のモックを印刷して組み立てのしやすさを確認しました。
- マウスモジュールは2枚の基板で構成する予定でしたが、箱が一体型になっていると箱の奥でモータや基板を固定する作業がやりづらいことがわかりました。
5回目
- 外装を縦に3分割して、重箱のように重ねられるようにしました。
- 主要な部品やコネクタ、基板が組み立て中に干渉しないことを確認できました。
完成した外装
以上のような試行錯誤をして外装が完成しました。
(以前の記事でも掲載しましたが、自分のマウスにとても愛着が湧いているので何度でも貼ります!)
以上、試行錯誤のサイクルを回してみて、非常に勉強になりました。設計のミスに早く気づいて修正できますし、Fusion360や3Dプリンタなど道具の使い方も反復することで効率よく勉強できたと思います。3Dプリンタでなにか作るときは、フィラメントを節約したくなる気持ちを乗り越えて何度も出力してみることをおすすめします。
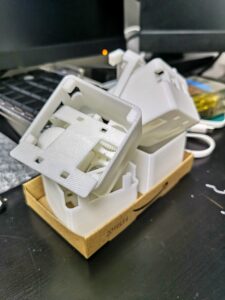
試行錯誤中の外装。もったいなくて捨てられない…