こんにちは、しおたにです。
前回ようやく基板を発注しました。
手元に届くまで1週間以上はかかるので今のうちに部品製作を進めていこうと思います。
おさらい
さて、当シリーズでは実に1年ぶりになる3Dモデルの登場です。
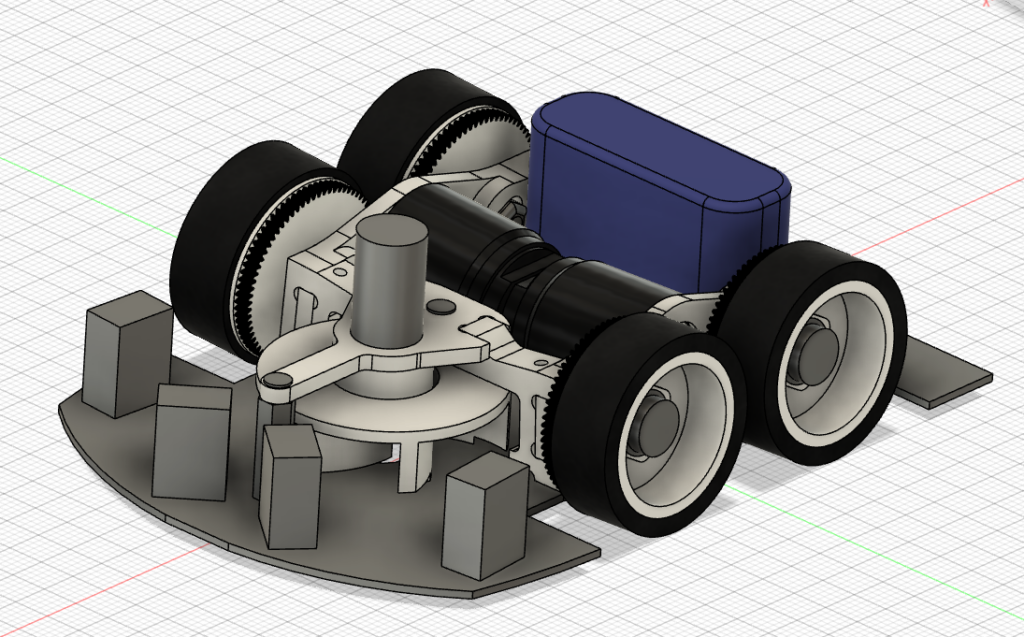
このような構造になっていました。
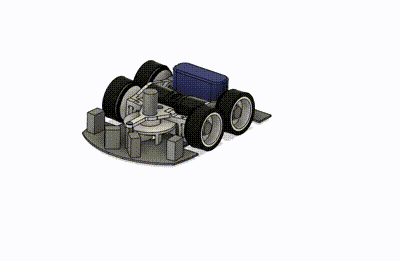
Fusion360でのモデリング過程は以下およびその近辺の回で紹介しています。
設計の流れをもう一度
部品製作を始めるにあたり設計の流れを確認しておきましょう。
ざっくりですが、今回は以下のように進めてきました。
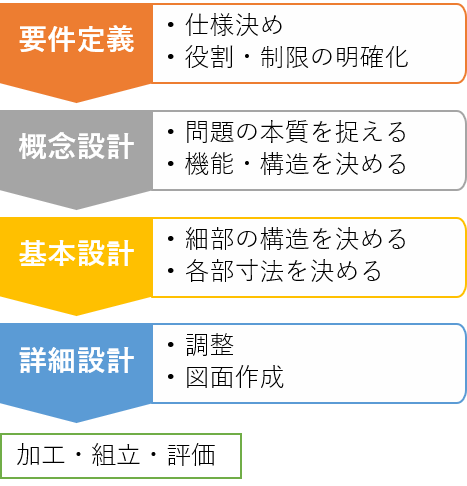
詳しくはこちらの回をご覧ください。
そして、このうちの「要件定義」「概念設計」「基本設計」についてはこれまでの回で紹介しています。
詳細設計
これまでの続きとなる「詳細設計」から始めていきたいと思います。
詳細設計はこれまで設計してきたものを具現化するため、諸々の準備を行うフェーズになります。
加工のための図面作成や細部の調整が含まれます。
加工環境の確認
ここで一度加工環境の整理をしておきましょう。
作りたくても持っていない、用意できない加工環境がある場合はその加工を断念するか工夫を凝らす必要があります。尤も最近は部品製作サービスが充実しているのでそういったことはあまりないと思いますが。
今回使用できる加工環境は以下の通りです。(これらを全て使うわけではありません)
- 卓上CNCフライス
- 3Dプリンタ
- ボール盤
- 卓上旋盤
- コンタマシン
- 手動ベンダー
- ミスミmeviyやDMM.make等への部品製作サービス
- バイスや定盤など手動加工工具
- ねじ切りタップや弓のこ、やすりなどの加工器具
これまで紹介してきた通り、卓上CNCフライスをメインに加工していきます。
加工する部品を確認
今回はほぼすべての部品加工で卓上CNCフライスを使用します。
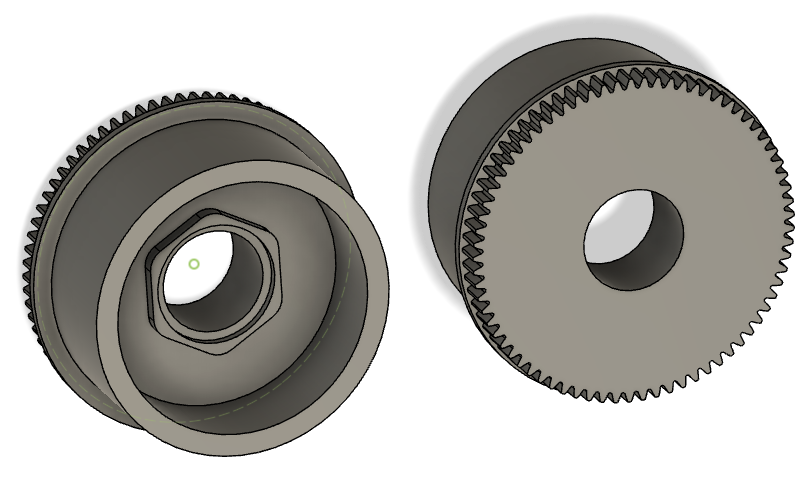
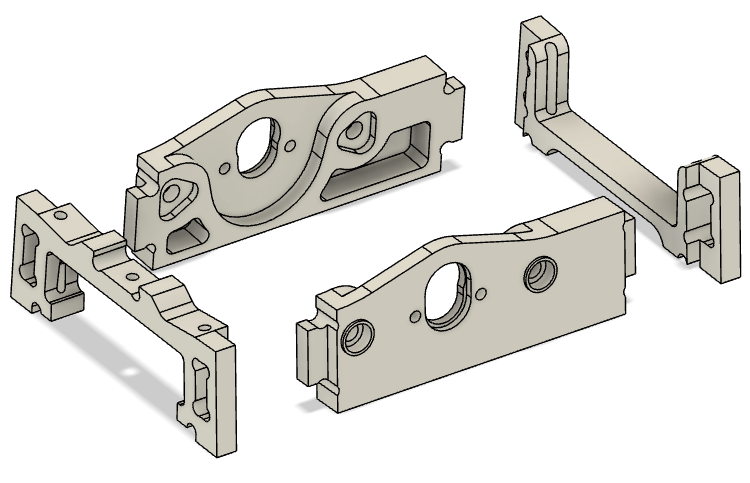
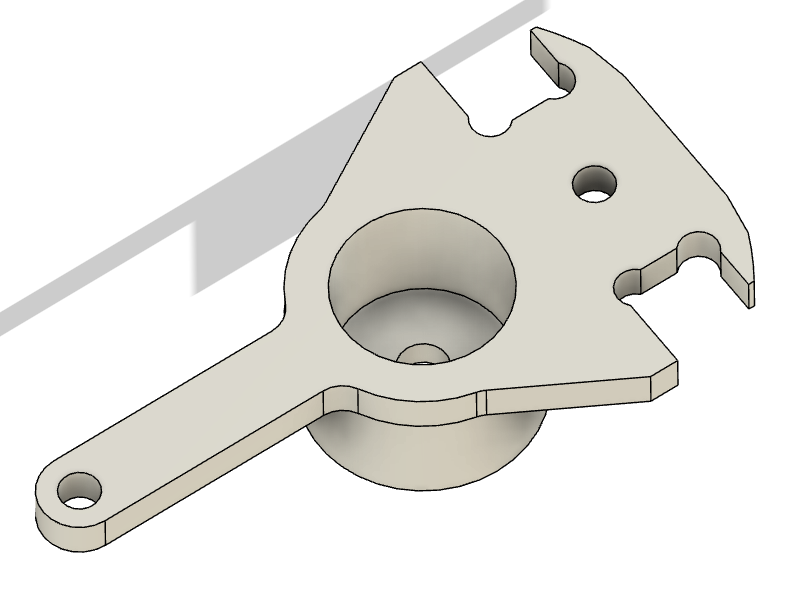
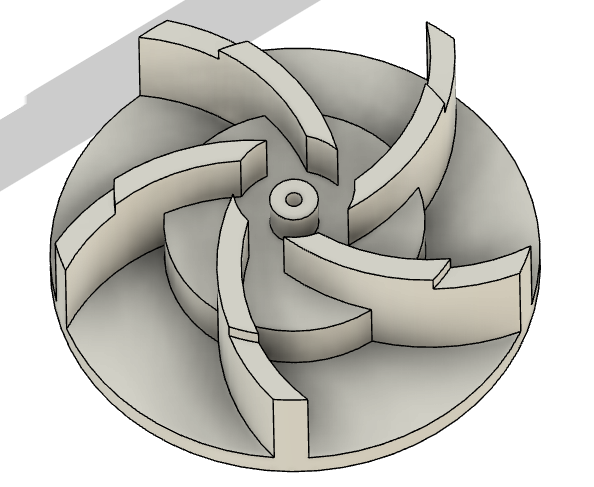
フライスで加工するにはいくつか制限がありますが、「要件定義」フェーズで洗いだした制限のうちに含まれていたので、これまでの設計フェーズにおいてもフライス加工を意識した形状にするようにしてきました。(↓の回とか)
これから各部品を加工する過程と、そのための準備について紹介していこうと思います。
長くなりそうなので一旦区切ります。