こんにちはショウです。
前回、回路図を引いたので次はアートワークをしたいのですが、その前に基板外形を決定する必要があります。
そのために今回は3DCADで機体設計をしていきます。
基本構成
機体構成はPart1に設定したとおりに吸引ファンを使い、タイヤ配置は変則四輪で作成します。
基板外形を決めるためには
- モータマウント形状
- ホイール形状
- コネクタ、スイッチ等のサイズ
- 壁センサの配置位置とサイズ
あたりの情報が必要になります。
最初に色々なマイクロマウスの基板形状を見てみるとこのような形状が多いです。
先端を丸くして、タイヤの部分を凹ませた構造です。
先端を丸くしているのは壁への接触時にクラッシュしにくくするためです。先端が丸くなっていると柱に接触しても基板に沿って滑ってくれるので引っかかって止まりにくくなります。
タイヤの凹み部分も壁との接触を考えて基板の横にタイヤが飛び出さないように幅に合わせて凹ませます。
今回の機体の基板も同じような形状で作成していきます。
モータマウント
大雑把な形状を決めたら、モータマウントを設計していきます。
モータマウント周りのギアの設計はしおたにさんのブログが参考になります。
ギアサイズはタイヤのサイズを超えられないので、ホイールのギアはモジュール0.3の36歯、ピニオンはモジュール0.3の10歯にしました。前の機体はピニオンが9歯で毎回当たる歯が同じになることに気がついたので10歯に変更しています。互いに素ではないですが大きく変更ができないので妥協です。
歯数の少ないピニオンやタイヤのサイズに対して小さいギアを使うとモータ軸とホイールが干渉するので、3DCADを使って干渉を確認してから決定しています。
バックラッシを考慮して軸間距離は基準円の半径の合計+0.12mmで設計しています。この数値は旧機体から流用しています。旧機体では最初0.05mmにしましたが、近すぎてうまく回転しなかったため、大会の際にマイクロマウス競技の出場者に相談してこの数値になりました。
大会時に確認の方法として、Fusion360の接触セットの有効化をして回してみるという方法を教えてもらいました。ギアを作成してからの方法ですが、CAD上で回してみると軸間距離がずれていると無理やり動かしているような動作し、適切な距離だときれいに回転します。
エンコーダはタイヤの軸に取り付けた磁石に対してICを垂直に取り付ける必要がありますが、はんだ付けだけで垂直を出すのは難しいです。メイン基板に穴を開けて垂直を出す方法もありますが、ドリルで穴を開けた際のフィレットが気になるので、穴を開けずに、マウントを使って位置出しをしています。
エンコーダ基板をモータマウントに押し付けて垂直を出すので、磁石をモータマウント内部に入れる必要があり、モータマウントの構造が少し複雑になります。
モータマウント内に磁石を配置する方法はこちらのブログを参考にしています。
モータマウントの内部に磁石を配置するのですが、磁石の隣には当然ですがモータがあります。モータの内部には磁石があるのでそのままだと互いに引き合ってしまい、きれいに回転しなくなります。この対策としてエンコーダの磁石のまわりに鉄スペーサーを入れて磁気をカットする方法がよく使われます。今回も鉄スペーサーを使って磁気をカットしています。
中に入れる磁石やスペーサー、磁石マウント、車軸の平行ピンと固定用のベアリング、タイヤとホイールのサイズを確認して、ホイールからの距離を計算しながらベアリングの位置や磁石ホルダーのサイズを決定してマウントを作成しました。
ベアリングの部分はマウントから飛び出す形にして、ホイールの内部に入る形状になります。
モータマウント内部で磁石や磁石マウントが干渉が起きないように調整をしていきます。ここで忘れそうになることとしてはエンコーダICの存在です。エンコーダICの厚さ分とクリアランスを考慮して寸法を決めます。モータマウント内部にエンコーダ基板面から、エンコーダIC、磁石までのクリアランス、磁石が入ります。
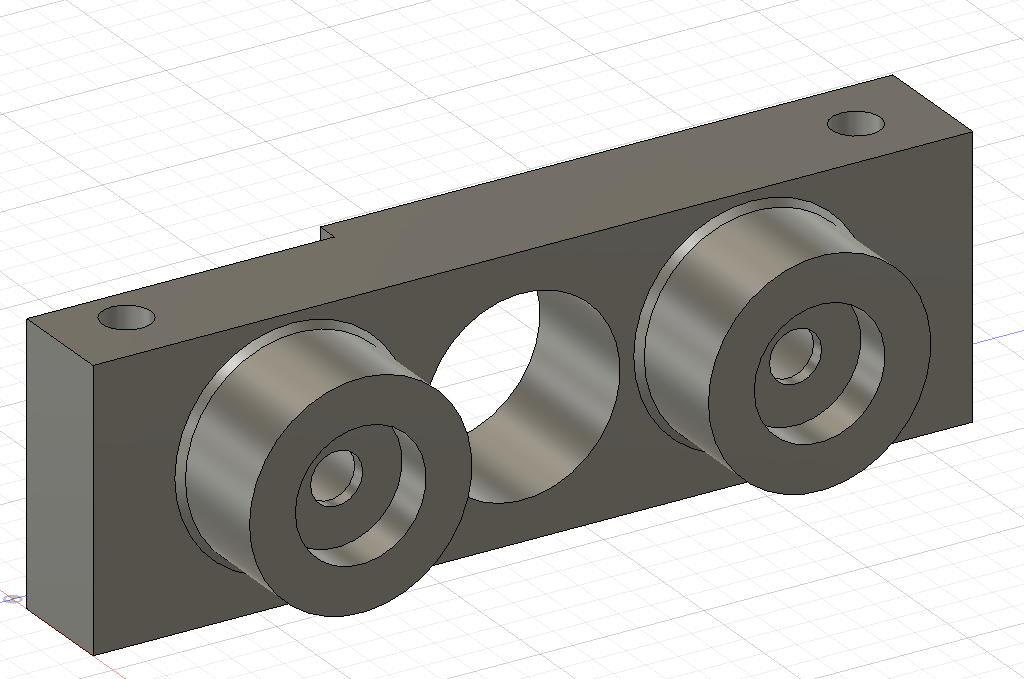
モータマウント全体図
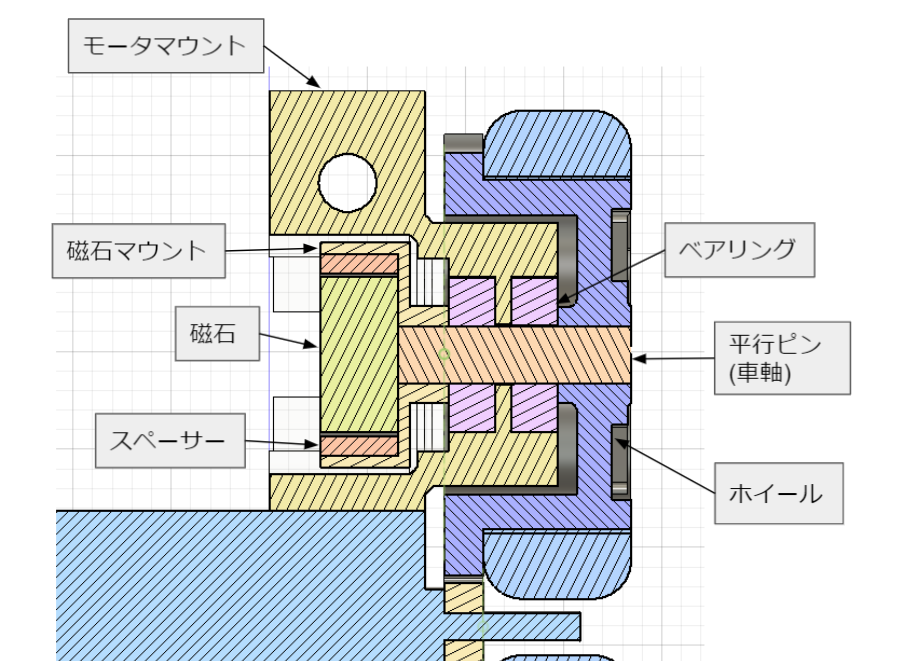
モータマウント内部
マウントの構造が決まったら必要な部品と配線を通せるだけの場所を確保できるサイズのエンコーダ基板の形と基板をはめ込む凹みを作っておきます。今回モータマウント内部のスペースがギリギリだったため、基板の凹みが0.1mmしかありませんが、位置と垂直出しはできるので問題ないと判断しました。
下側が凹ませてあるのは、半田をマウントに押し付ける側にもつける必要があったので、半田とマウントが干渉しないようにするために凹ませています。
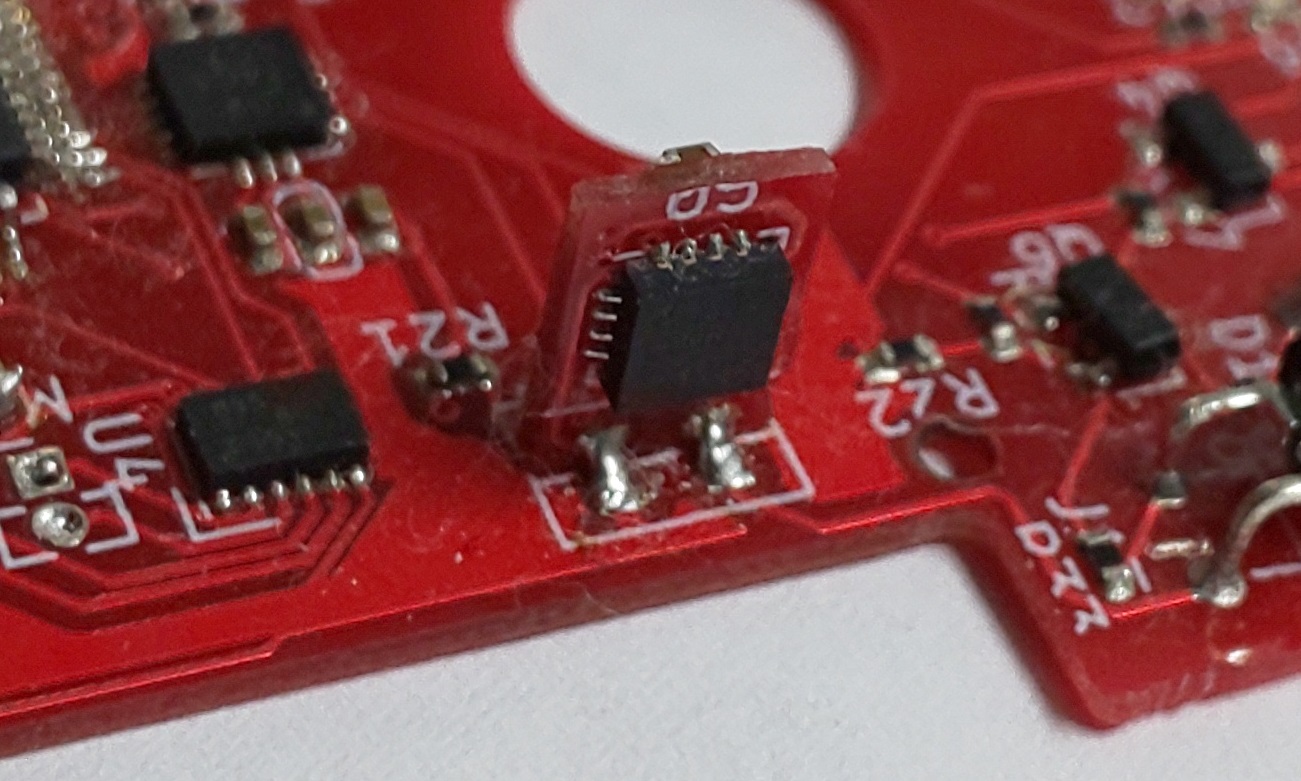
エンコーダ基板イメージ
また、今回は吸引ファンを搭載するので吸引ファンの固定も考える必要があります。別部品として吸引ファン用のマウントを用意することもできますが、固定部が小さくなって不安定だと思いモータマウントと一体にして設置面を確保しています。そのため、モータマウントを少し前方に長くすることにしました。
今回モータマウントはDMMの3Dプリンター出力サービスのアクリルで作成するので、DMMの作成ルール内で作る必要があります。厚みが0.3mmまでしか作れないので0.3mm以下になる場所が無いように気をつける必要があります。
エンコーダを取り付けない側のマウントが凹んでいるのはバッテリーのスペースが足りなくなったので、あとから削りました。
ベアリングやモータなどの部品は作成しておいて、アセンブリをして干渉チェックを行っておきます。アセンブリで都合の悪い部分が見つかったら、都度寸法を調整していきます。
失敗
今回、磁石のマウント部分で設計ミスをしました。エンコーダの磁石は大きい方が回転時の値が安定します。そのためφ4の磁石を使い内径4.2mmのスペーサーに入れようと最初に設計してました。内径4.2なのでクリアランスが0.1mmしかない設計になっていました。この時点でDMMでは作成不可能です。これに気がついたのがDMM発注の直前で、すでにφ4の磁石とスペーサーは注文したあとでした。この時点で大会までの時間も残ってなかったので磁石とスペーサーの隙間をテープで埋めてスペーサーの外側に固定用のケースを作る構成に変更しました。その結果モータマウントの磁石スペースの穴も大きくなり、モータマウント側も外側のホイール部分との厚みがなくなって設計変更するはめになりました。今回は面取りなどを使ってなんとか寸法を確保しています。(一度気づかずにDMMに出して作成不可のメールをもらいました。)
結果位置出しは正確にならず、はめ込みも甘いという状態となってしまいました。修正できてないのは時間不足です。ここは後日修正する予定です。
今回はここまで、次回ホイールなどを作成して基板形状を決定します。